History
Plasma Transferred Arc Welding System was invented by Robert M. Gage in 1953 and patented in 1957. He also invented Plasma Arc Cutting (PAC) at the same time. Both technologies have become a very productive way to weld and cut metal parts, both by hand and by robots. It’s main advantages is there is hardly any distortion because of very low heat input to the work pieces.
What is PLASMA?
PLASMA is the fourth state of matter after solid, liquid and gas.
In case of Water: More heat is added, it will be changed to plasma
In Plasma Transferred Arc System, inert gas like Argon is used. Inert gas flow through high electrical arc between electrode (-) and nozzle constriction (+). This gas will be ionized. In ionized state, atom of inert gas will be broken into electron (-) and cation (+). A typical value of temperature obtained in plasma jet is about 28,000 ºC, compared to about 5500 ºC in ordinary electric welding arc.
Principle of Operation (Equipment)
Plasma Arc
Plasma arc is created by ionization of Argon gas passing through the electric arc formed between tungsten electrode (-) and the welding torch or nozzle (+).
Second electric arc called Transferred Arc, happened between electrode (-) and substate or work-piece (+). This second arc will further increase the temperature between 8,000 ºC and 18,000 ºC.
Powder Feeder
Powder filler metal is continuously feed on the substate (work-piece) through the plasma arc. Inert gas like Argon help carrying powder feeding through.
Shielding Gas
Shielding Gas, can be Argon or other gases like Helium, Argon + Helium or Argon + Hydrogen, are used to shield the arc area to protect oxidation.
Cooling System
Cold water will be pumped into the nozzle to take out heat from the arc accumulated in the nozzle. This hot water will be treated by chiller and send back to the nozzle.
Power Supply
Power Supply will change main electrical current to different currents suitable for arcing, feeding motor, water chiller and control system.
Advantages
- Very low dilution with the base metal. Reaching the hardness of the deposited material in a single layer.
- Good bonding, bond strength about 65,000 psi (as welding on the substrate.
- Low heat Addition. High working speed reduce the thermal addition to the work piece. With the same deposition rate, comparing with other fusion welding, the metallurgical structure is much better. The energy efficiency is very high, for example 12 kW of electric energy are enough to deposit approx. 6 kg/hour of metal.
- Flexibility of the system. Constance of result and easy automation providing high degree of reproducibility.
- Small Heat-Affected Zone (HAZ).
- Precise metering of metallic powder feed stock, resulting in lesser powders used.
- Produces smooth deposit that close to the final geometry. Reduce required machining time.
- Produces alloy deposits that are tougher and more corrosion resistant than counterparts laid down by GTAW or FCW processes.
- Low Pollution. Less welding fumes than traditional welding methods.
Applications
1. Valves for automotive, marines, and petrochemical industries.
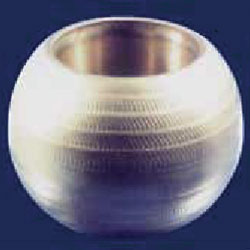
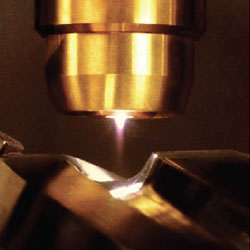
2. Screws in plastics, wood, oil industries.
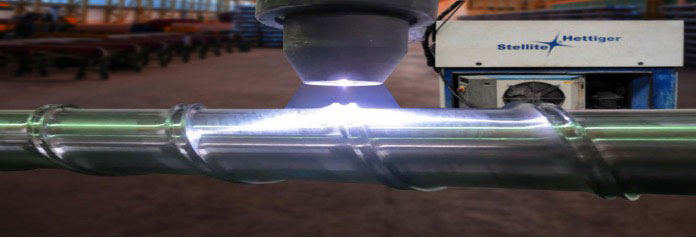
3. Industrial rollers.
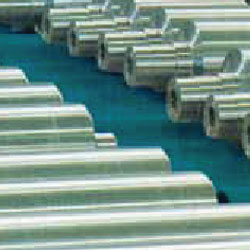
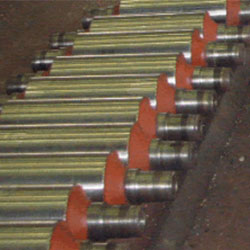
4. Molds and plungers in glass industry.
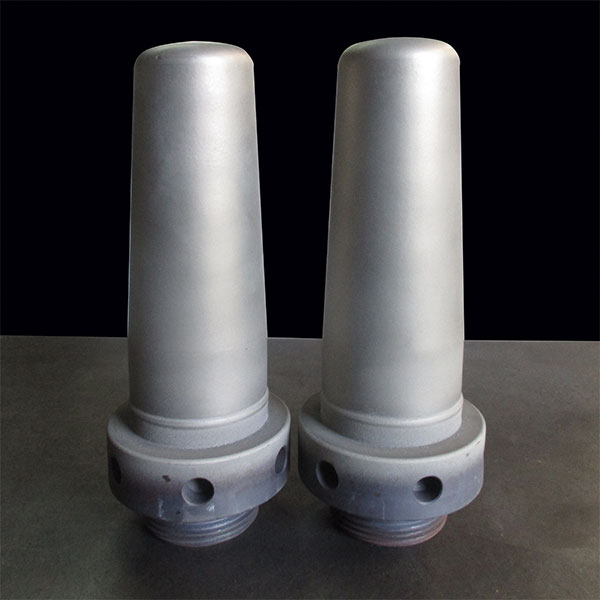
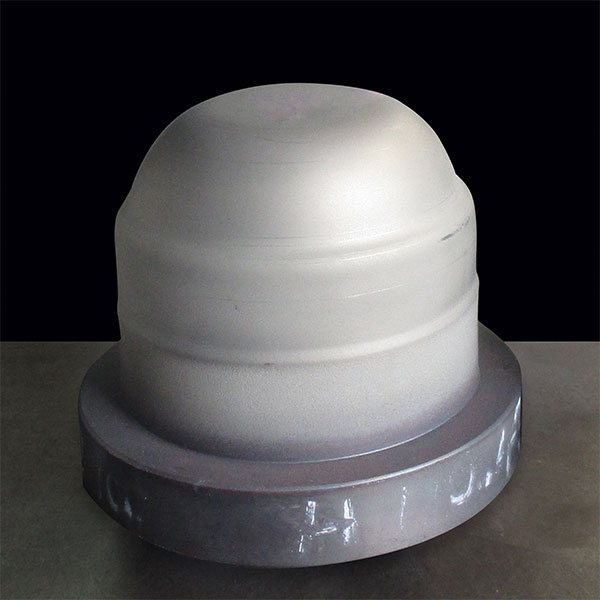
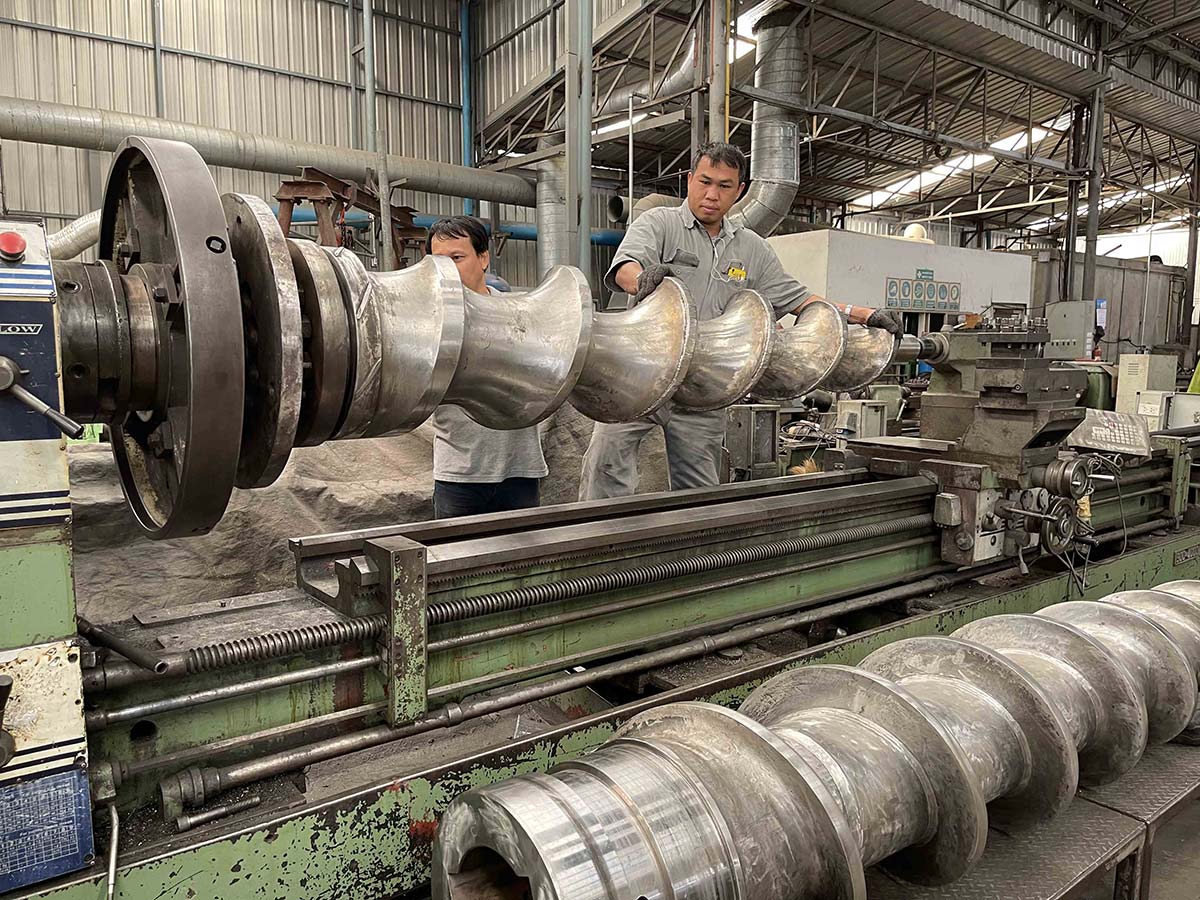